quick
delivery
produced to
highest standards
Delivery from stock
The material 17 4PH stainless steel is a rustproof, martensitic, hardenable Cr-Ni-Cu steel with high strength and toughness.
For US customers: -> Our Warehouse in Beaumont Texas
International identifiers
X5CrNiCuNb16-4 / X5CrNiCuNb17-4-4 | AISI – 630 | UNS S17400 NACE MR0103 / MR0175 | AFNOR Z7CNU15-05 / Z7CNU17-04 ASTM A564 17-4PH / A564M-13 | JIS SCS24 / SUS630
Chemical composition
174PH | C | Si | Mn | P | S | Cr | Mo | Ni | V |
min. | bis | bis | bis | bis | bis | 15 | bis | 3 | |
max. | 0,7 | 0,7 | 1,0 | 0,04 | 0,03 | 17,5 | 0,6 | 5 |
17-4PH | Al | Cu | N | Nb | Ti | other |
min. | 3,0 | 5xC | ||||
max. | 5,0 | 0,45 |
Particularities:
Available in ESU quality
Very good corrosion resistance, strength & toughness
Excellent notched impact strength – even in the low-temperature range
Proven resistance to stress corrosion cracking
Triple attestation (17-4PH | 1.4542 | 1.4548)
Ultrasonically tested material to ASTM & NACE standards
Suitable for use in maritime environments
Available in swap state:
Condition H1150 (Rm > 930N/mm2)
Condition H1025 (Rm > 1070N/mm2)
Condition H900 (Rm > 1310N/mm2)
Condition A (Rm max. 1200N/mm2) max. hardness of 363 HB.
Machining and subsequent hardening possible.
Weldability:
The material 17 4PH offers excellent welding properties for various welding processes (TIG, electric arc welding). Welding should be carried out in the solution annealed condition.
Heat treatment:
In the solution-annealed condition (A), the material 17-4 can develop a wide range of properties and be adjusted to very good notched impact strength through appropriate heat treatment. In contrast to normal, hardenable materials, the material 174 PH can already be hardened to the desired final property in one operation.
The table Aging (age hardening) gives an overview of the required times and temperatures.
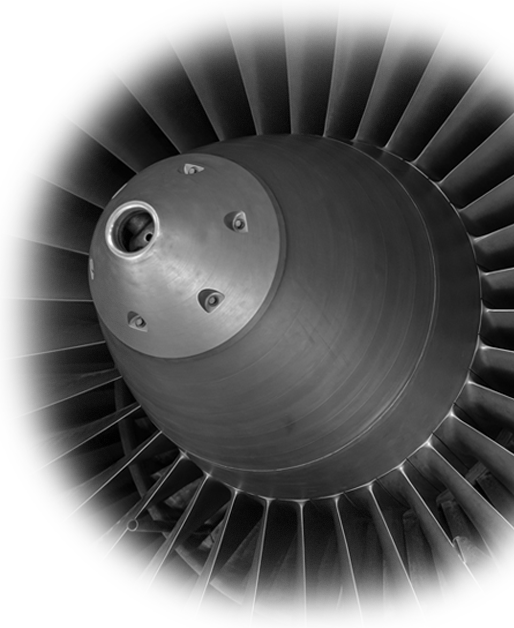
Age hardening
Condition | Temperature in °C / °F | Curing Time (hours) | Cooling |
H900 | 482 °C (900 °F) | 1 | Air |
H1025 | 552°C (1025 °F) | 4 | Air |
H1150 | 621 °C (1150 °F) | 4 | Air |
Cold forming: possible
Hot forming: possible
If you need further information on the subject of cold forming and hot forming – our technical sales department will be happy to advise you.
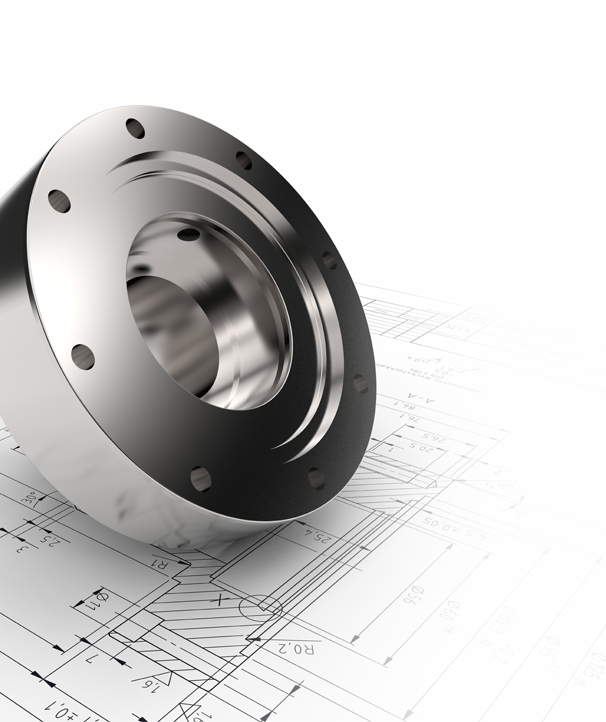
Area of application:
The material grade 17 4PH is used, for example, for cover discs in compressor construction, valve blocks and for fittings (valves, bushings, etc.) in the petroleum and chemical industries, which require high hardness and corrosion resistance at temperatures of up to 600°F (316°C ) require. The material can be used in maritime environments. For permanent use in standing sea water, however, additional protection is recommended to prevent crevice corrosion.
Physical Properties:
Density in kg/dm3: 7.8
Electrical resistance at 20°C in (Ω mm2)/m: 0.71
Thermal conductivity at 20°C in W/(m K): 16
Specific heat capacity at 20°C in J/(kg K): 500
Mechanical properties at room temperature
according to ASTM A564:
(forging up to 300 mm)
Condition | Hardness | 0,2% proof stress N/mm² min | Tensile strength N/mm² | Elongation A % min. | Reduction of area % min. | Impact strength (ISO-V) J min. | |||
L | Q | L | Q | L | Q | ||||
H900 | 400-450 | 1170 | 1310 | 8 | 6 | 38 | 25 | 20 | 10 |
H1025 | 330-390 | 1000 | 1080 | 12 | 10 | 45 | 30 | 25 | 20 |
H1150 | 270-340 | 750 | 930 | 16 | 13 | 50 | 38 | 42 | 32 |
L=Longitudinal; Q=Transverse
Why saw cut?
The mechanical processing of the material with the band saw results in a significantly lower unintentional deformation and hardening of the material for the existing structure, in contrast to flame cutting.
Thus, the workpiece processed by the saw already has a homogeneous structure at the edge, which does not change in the continuation of the material. This circumstance enables the immediate finishing of the workpiece with milling or drilling, without having to carry out another soft annealing or similar work step beforehand.
Contact us now for more information
America
Karol Borycki
+1 409 2395919
Germany
Antje Schroeder
Polska
Natalia Podraza
Spain
Gaby Path